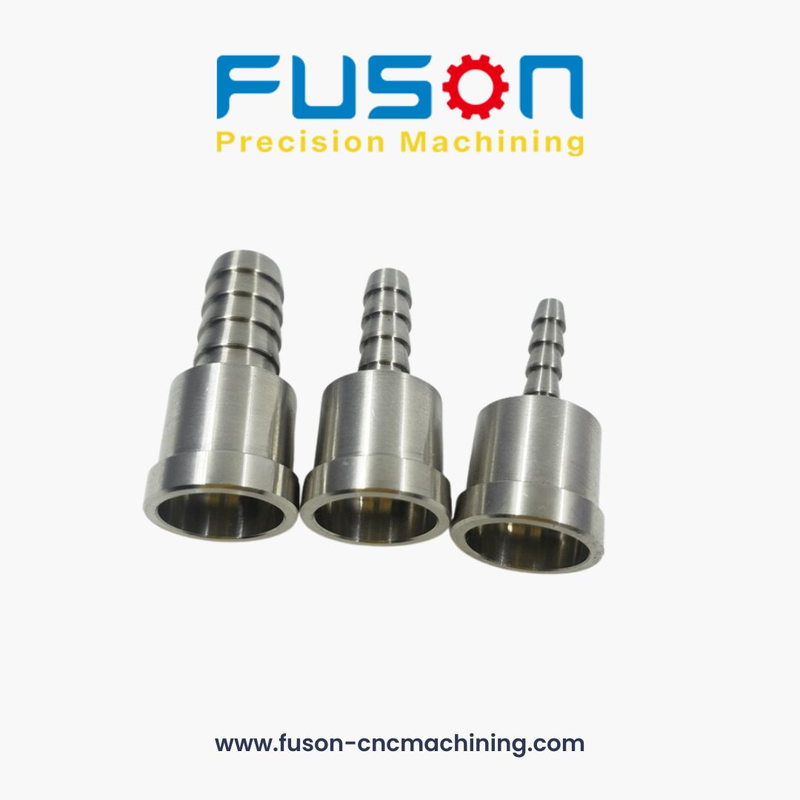
Increasing Productivity and Quality with Accurate CNC Milling Methods
Welcome to our blog post about using
CNC milling precision techniques to increase quality and efficiency! It's critical to deliver high-quality outcomes quickly in the competitive industrial sector of today. This is the application of CNC milling. We can help you regardless of your level of familiarity with this cutting-edge machining technique or your initial exploration of its possibilities.
We shall explore the realm of CNC milling in-depth in this post and reveal the mysteries underlying its exceptional advantages. We'll also share some cutting edge methods that will help you achieve unprecedented precision machining results. Prepare for an educational trip that will transform your production operations, from boosting productivity with multi-axis machining to enhancing precision with appropriate tool selection.
Thus, take a seat, get a cup of coffee (or tea, if you prefer), and allow us to take you through the fascinating world of precision CNC milling procedures. Let's get going!
Knowing CNC Milling and Its Advantages
Computer Numerical Control (CNC) milling is a state-of-the-art machining technique that uses computerized controls to create precise and complex pieces. When it comes to accuracy and consistency, CNC milling is unmatched compared to older manual milling techniques. High degrees of precision can be achieved with little human intervention by manufacturers thanks to the ability to put complex designs into the machine software.
The adaptability of CNC milling is one of its main benefits. This method can easily handle a wide range of materials, from plastics and composites to metals like steel and aluminum. Because of its adaptability, it is perfect for a wide range of industries, including electronics, automotive, aerospace, and more.
Not only is CNC milling extremely versatile, but it's also very efficient. Using CAD/CAM software to automate the machining process using pre-programmed instructions, businesses can save a great deal of time on production runs without sacrificing quality. Additionally, because CNC milling is automated, it reduces human error—a typical problem in manual operations—which lowers waste and boosts efficiency all around.
And there you have it - a quick overview of CNC milling and all of its advantages. The subsequent parts will delve into sophisticated methodologies that augment accuracy and efficacy in this pioneering manufacturing process.
Innovative Methods for Superior CNC Machining
Cutting-edge methods and approaches are necessary to provide CNC milling results that are of the highest caliber. These methods enable more accuracy and efficiency and go beyond the fundamental procedures. These are some essential strategies that can improve the caliber of projects involving CNC milling.
Making the right tool selections to maximize accuracy is one crucial tactic. The success of a project can be significantly impacted by selecting the appropriate tools, such as end mills with particular geometries or coatings. An operator can guarantee accurate cuts with few mistakes by choosing tools that are appropriate for the material being machined and taking into account variables like feed rate and cutting speed.
Finding the right feeds and speeds to achieve smooth surface finishes is another important factor. Precisely setting these parameters minimizes burrs on completed parts, avoids tool wear, and lessens vibrations. Improved surface finishes that meet or surpass necessary criteria can be achieved by adjusting feeds and speeds in accordance with the characteristics of the material.
In terms of CNC milling operations' efficiency, multi-axis machining has a number of noteworthy benefits. Accurate and speedier production of complicated designs is possible when several axes are used concurrently. This method cuts production time without compromising accuracy by enabling simultaneous cutting from various angles or orientations.
Utilizing these cutting-edge methods in CNC milling operations allows manufacturers to improve productivity and quality. When optimal feeds and speeds are combined with multi-axis machining, excellent results are guaranteed at a lower production time, which in turn increases customer satisfaction.
Optimizing Precision with Appropriate Tool Selection
The right tool selection is a critical component that can significantly effect accuracy when it comes to
CNC milling services. Selecting the appropriate tools for your machining requirements can significantly impact the attainment of accurate and superior outcomes.
Take into account the materials you will be working with first and foremost. For best results, different kinds of cutting tools are needed for different materials. Using a tool made especially for the material—be it plastic, steel, or aluminum—will help to enhance accuracy.
Be mindful of the geometry of the tool. Chip evacuation and heat dissipation are significantly influenced by elements like helix angle and flute shape. Choosing tools with effective chip removal capabilities will enhance overall precision and stop chips from interfering with the machining process.
Think about the coating on your cutting instruments. By lowering wear and friction, coatings like diamond-like carbon (DLC) and titanium nitride (TiN) can extend the life of tools. This keeps tolerances tight while guaranteeing steady performance over extended production runs.
You can greatly improve accuracy during CNC milling processes by carefully selecting the appropriate tools based on material compatibility, geometrical features, and coatings suited to your particular application requirements.
Obtaining Even Surface Finishes with Appropriate Feeds and Speeds
Using the right feeds and speeds is one of the most important things when it comes to CNC milling clean surface finishes. These variables control how rapidly the cutting tool turns and moves across the material. Manufacturers can attain superior finishes, minimize burrs, and lessen roughness by fine-tuning these parameters.
Striking a balance between too slow and too rapid is crucial when it comes to feeds. An inadequate feed rate might lead to poor chip evacuation and an excessive build-up of heat. Conversely, an excessively high feed rate may result in chatter marks on the workpiece or tool breakage. Achieving the ideal material removal while preserving surface quality requires determining the proper feed rate.
Another important factor in obtaining smooth surface finishes is speeds. While higher spindle speeds enable higher cutting rates, they may also cause vibrations that degrade the quality of the finish. Longer machining times may be the consequence of using lower spindle speeds, which offer more stability. To find the sweet spot that provides efficiency and superior surface finishes, it's critical to test out various feed and speed combinations.
CNC milling operators can maximize process efficiency without sacrificing quality by carefully choosing feeds and speeds that are suitable for each unique task!
Enhancing Productivity with Multi-Axis Machining
Among the best methods for raising the caliber and productivity of
CNC milling is multi-axis machining. Multiple axes can move simultaneously with this approach, making it possible to precisely make complicated and complex shapes. Manufacturers can decrease setup times, do away with the necessity for repeated setups or part repositioning, and eventually boost production by employing multi-axis machines.
Comparing multi-axis machining to typical three-axis milling reveals a number of benefits. Because it gives operators more freedom when positioning their tools, they can more readily reach locations that are challenging to access. This decreases the possibility of tool collisions or insufficient cutting angles, which improves accuracy and surface finishes.
In addition, multi-axis machines allow a workpiece to be machined simultaneously on several surfaces without requiring manual repositioning. This reduces mistakes brought on by alignment problems and gets rid of part handling delays. A reduction in manufacturing process interruptions results in a major decrease in overall production time.
Multi-axis machining not only improves productivity but also creates new opportunities for creative design. The capacity to rotate a workpiece in many directions allows for the production of intricate geometries that would be difficult or impossible to achieve using traditional milling methods alone. Manufacturers are able to create distinctive forms and shapes while upholding strict quality control and tight tolerances.
Partnering with a seasoned CNC milling service provider that has cutting-edge machinery and knowledge in this field is essential to maximizing the benefits of multi-axis machining. Their expertise will guarantee that the best programming strategies are applied for the demands of any unique project.