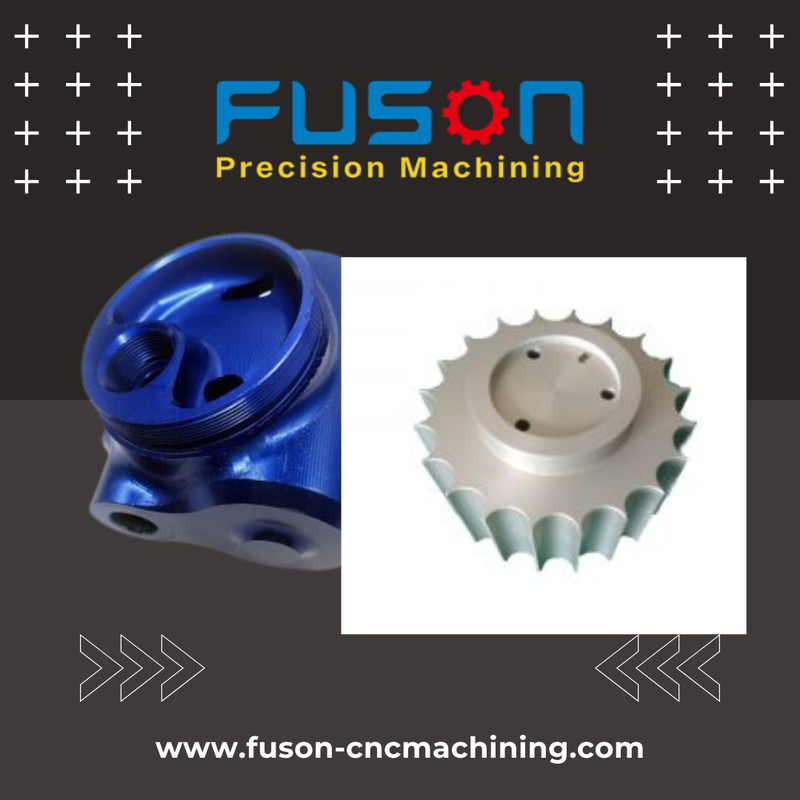
Precision CNC Milling: A Game-Changer in Aerospace Engineering
Precision CNC milling has revolutionized the aerospace engineering industry, taking it to new heights of innovation and efficiency. With its ability to produce intricate parts with unparalleled precision, CNC milling has become a game-changer in the world of manufacturing. If you've ever wondered what exactly CNC milling is and how it impacts aerospace engineering, this blog post is for you! We'll dive into the fascinating world of precision machining and explore the advantages it brings to this dynamic field. So fasten your seatbelts as we take off on an exciting journey through precision CNC milling in aerospace engineering!
Understanding Precision CNC Milling
Precision CNC milling is a manufacturing process that involves using computer numerical control (CNC) machines to remove material from a workpiece with extreme accuracy and precision. These machines are equipped with cutting tools that can move in multiple axes, allowing for the creation of complex shapes and designs.
At its core, CNC milling relies on computer programming to guide the machine's movements and operations. The instructions are fed into the machine through specialized software, which translates them into precise movements of the cutting tools. This level of automation ensures consistent results and reduces human error, making it an ideal choice for industries like aerospace engineering where precision is paramount.
The process begins with designing a 3D model of the desired part using computer-aided design (CAD) software. This model serves as a blueprint for the CNC machine, detailing all dimensions and specifications required. Once programmed, the CNC mill starts removing material from the workpiece by rotating at high speeds while simultaneously moving along different axes according to the programmed instructions.
Precision CNC milling has revolutionized manufacturing processes in aerospace engineering by offering unparalleled accuracy and repeatability. With this technology at their disposal, engineers can create intricate components such as turbine blades or aircraft structural parts with exceptional precision that was previously unattainable through traditional machining methods.
What is CNC Machine Milling?
CNC machine milling is a revolutionary technology that has transformed the manufacturing industry. It stands for Computer Numerical Control, which means that the machines are controlled by computer programs to precisely shape and cut materials with utmost accuracy.
In simple terms, CNC milling involves removing material from a workpiece using rotating cutting tools. The process starts with creating a digital design or blueprint of the desired part. This design is then converted into code that controls the movement of the machine's axes, guiding it to carve out the required shape.
One of the key advantages of CNC machine milling is its ability to produce complex and intricate parts consistently and efficiently. The precision achieved through this process ensures tight tolerances and eliminates human error, resulting in high-quality components for various industries including aerospace engineering.
A Guide to CNC Milling
CNC milling precision is a widely used technique in various industries, including aerospace engineering. But what exactly is CNC milling? Put simply, it is a process that uses computer numerical control (CNC) machines to remove material from a workpiece and create complex shapes with high precision.
To guide you through the CNC milling process, here are three key steps involved. First, the design of the part or component is created using Computer-Aided Design (CAD) software. Next, this design file is converted into machine-readable code called G-code. This code contains instructions for the CNC machine on how to move and position the cutting tool. Once the setup is complete, the CNC machine starts removing material from the workpiece following the programmed path.
Precision plays a crucial role in CNC milling as it ensures accurate results. Achieving precision requires careful planning and consideration of factors such as tool selection, feed rates, spindle speed, and cutting parameters. The use of advanced technology allows for tight tolerances and intricate details that meet aerospace industry standards.
What is Precision Machining?
Precision machining involves the use of advanced machinery to create intricate and highly accurate components. It is a process that requires skill, precision, and attention to detail. The goal of precision machining is to produce parts with extremely tight tolerances, ensuring that they fit together seamlessly and function flawlessly.
One key aspect of precision machining is the use of computer numerical control (CNC) technology. This allows for precise control over the cutting tools, resulting in consistent and repeatable results. CNC machines can perform complex operations such as milling, drilling, turning, and grinding with incredible accuracy.
Another important factor in precision machining is the selection of materials. High-quality metals such as aluminium, stainless steel, and titanium alloys are often used due to their strength and durability. These materials undergo various processes such as cutting, shaping, drilling or grinding until they meet the required specifications.
In aerospace engineering particularly, precision machining plays a critical role in manufacturing aircraft components like turbine blades or engine housings which require extreme accuracy and reliability in order to withstand harsh conditions experienced during flight. With advancements in CNC technology continuing to push boundaries within this field it's clear that precision machining will remain an essential tool for aerospace engineers well into the future.
Advantages of Precision CNC Milling in Aerospace Engineering
Precision CNC milling has revolutionized the field of aerospace engineering, offering a myriad of advantages that make it an indispensable tool for manufacturers. Let's take a closer look at some of these benefits:
1. Accuracy: One of the most crucial aspects of aerospace engineering is precision. With
CNC Machining, manufacturers can achieve unparalleled accuracy and consistency in their machining processes. The computer-controlled machines ensure precise measurements and eliminate human error, resulting in complex parts that fit perfectly together.
2. Efficiency: Time is money, especially in the aerospace industry where deadlines are tight and schedules are strict. Precision CNC milling allows for faster production rates by automating various tasks and reducing manual labour requirements. This efficiency translates into significant cost savings for manufacturers while maintaining high-quality standards.
3. Versatility: Aerospace components often have intricate designs and require diverse materials like aluminium, titanium, or composites to meet specific performance criteria. Precision CNC milling can handle a wide range of materials and accommodate complex geometries with ease, making it ideal for producing various aircraft parts such as engine components, wing structures, landing gears, and more.
4. Consistency: In aerospace engineering, consistency is key to ensuring reliability and safety across all manufactured components. CNC machines reproduce identical parts repeatedly without any deviation from the original CAD design specifications. This uniformity guarantees consistent performance throughout the entire fleet of aircraft.
5 . Innovation: Precision CNC milling opens up new possibilities for innovation within aerospace engineering by enabling engineers to push boundaries when designing cutting-edge technologies like lightweight structures or advanced aerodynamic shapes. These innovative solutions not only enhance aircraft performance but also contribute to fuel efficiency and reduced emissions.
6 . Cost-effectiveness: While precision CNC milling may require upfront investments in machinery and training programs, its long-term cost-effectiveness cannot be ignored. By minimizing errors during production processes and optimizing material usage through accurate programming techniques, manufacturers can significantly reduce waste levels while maintaining high-quality standards in aerospace manufacturing.